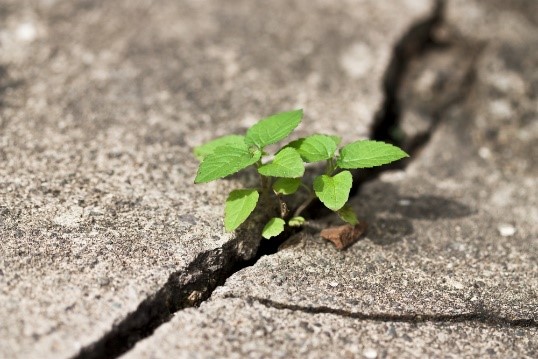
As home inspectors, we are often asked questions about cracking concrete. This guide will help you to explain some of the most common reasons why cracks develop in concrete slabs. While some cracking is inevitable in poured concrete, excessive cracking may (possibly) cause some problems with the home, it will definitely cause some problems (and questions) for the home inspector.
Most common reasons why cracks develop in concrete
1. Excess water in the initial mix
Concrete does require water to activate the mixture, but often an excessive amount of water is added to the mixture. This is typically done to make the concrete easier to install, but excess water can also reduce the strength of concrete. As the water in the mixture evaporates, the concrete hardens, dries and shrinkage occurs. The slab may normally shrink as much as ½” per 100 feet. The wetter the concrete, the more shrinkage that occurs and the more common the visible cracking.
2. Concrete drying too rapidly
There is a chemical reaction that occurs when the initial dry materials are combined with water, which allows the mixture to eventually change from a liquid to a solid state. As it dries, the strength of the concrete is increased. If it is dried on a proper schedule, the strength of the concrete increases, reducing the possibility of cracking. If the mixture is allowed to dry (cure) too quickly, the possibility of cracking dramatically increases. Typically, a poured slab should be allowed to cure (and the surface kept moist) for 7 days. Unfortunately, most contractors are under time constrains and cure the slab more quickly, which can lead to cracking.
3. Improper strength concrete mix for the specific job
Concrete comes in different mixtures/strengths for different applications. It is important that the proper mix be used for each application. This information is typically provided to the local concrete supplier, to ensure that the proper mixture is provided for the specific job.
4. Lack of control joints
All concrete will develop cracks as it cures. Control joints are placed in the slab to allow concrete to crack in specific areas instead of random cracks developing. Joints are typically installed at 2-3 times (in feet) the thickness of the slab. For example, 4-inch concrete should have control joints 8-12 feet apart. Lack of proper control joints often leads to random cracking of the slab.
5. Settlement cracks
Cracking may develop in the slab over embedded items, such as reinforcing steel or wire mesh, or close to forms or other hardened concrete (serving as a form). Cracks over reinforcement items may occur when the embedded items are too close to the surface of the slab and lack an adequate covering of concrete. These cracks typically follow the outline of the embedded items.
6. Other reasons
-Concrete was poured when temperatures are approaching freezing.
-Ground was not properly compacted prior to pouring concrete.
-Soil was not properly prepared prior to pouring concrete. Some areas of the country can have slabs poured directly on the ground, while other areas require extensive prep work, including the addition of fill and/or reinforcement bars or wires installed inside of the slab.
-Concrete was not properly vibrated during installation, resulting in trapped air pockets in the slab.
In most situations, the perception of the client is the most problematic issue when it comes to cracks in the concrete. While they may be unsightly, most cracks do not represent any structural concerns in a slab. While opinions vary, most experts believe that if a crack is not structural, is not too wide (in the range of 1/16” to 1/4") and is not leaking water, then it is acceptable. As home inspectors, our best practice is typically to point out the crack, document it in the report, and recommend monitoring of the area for any future changes.