Most people don’t think much about the electrical wiring hidden inside their walls, that is, until something goes wrong. It’s in our best interest, as professional home inspectors, to make sure that our clients know what type of wiring is present inside the walls of their home and to educate them regarding the pros and cons of the different types available.
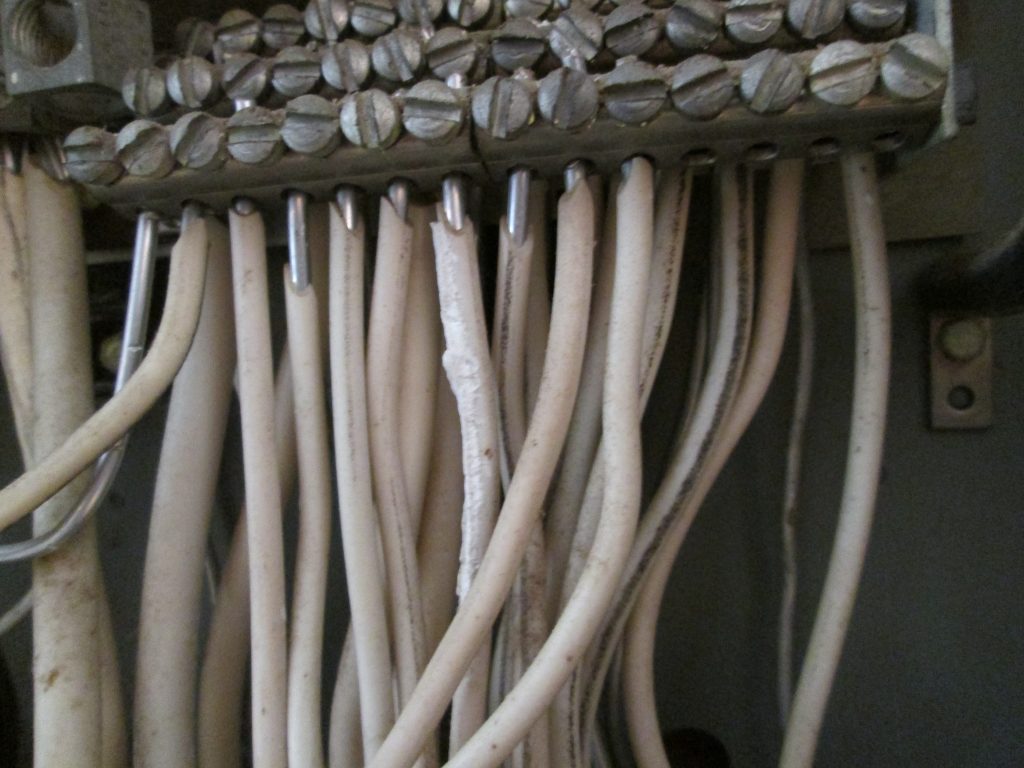
One of the biggest differences in residential electrical wiring would be the type of metal used to make the wires. We’re bound to encounter both copper and aluminum wiring while inspecting homes, and we should know enough about these materials to make informed statements to our clients regarding what to expect from their electrical system.
Copper wiring has been used since the 1820’s, with the invention of the electromagnet and the telegraph. While aluminum wiring has been used since the late 1800’s, as power companies utilized it while building their power transmission networks, it wasn’t until the 1960’s that solid branch aluminum wiring began to be used to wire homes in the U.S.
While aluminum and copper are both effective conductors of electricity, there are some important differences between the materials that affect how well they’ll perform in our homes. Obviously, we’re aware of the basic facts that copper is a better conductor while aluminum is a cheaper material, but a more in-depth understanding of the differences between these two conductors will enable us to provide more (and better) information to our clients. Hopefully we’re able to educate them enough that they can make a more informed decision about whether to purchase a specific home as well as provide evidence to protect us and our business if something bad happens in the future.
We’ve all heard that copper is a better conductor than aluminum, but do we know what that even means?
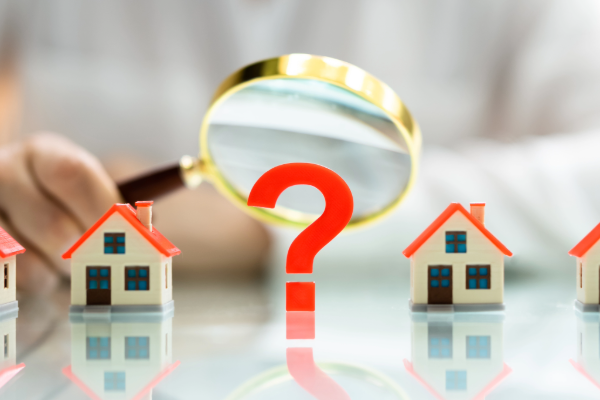
Copper boasts a higher electrical conductivity than aluminum, with a rating approximately twice that of aluminum. Conductivity is a measurement of the ability of a substance (wiring in this instance) to conduct electricity. The standard way conductivity is measured is in the units siemens per meter (S/m), which is where the manufacturer Siemens gets its name. The difference between the conductivity of copper and aluminum can be attributed to the atomic structure of the metals.
Electricity flows through the movement of electrons, and the fact that the electrons of copper atoms are more readily transferred between atoms than those of aluminum allows for a more favorable environment for electron mobility within the copper wire. The looser grip on copper’s outer electrons allows for easier movement in response to an applied electric field, facilitating a more efficient flow of electricity.
The higher conductivity of copper means that it can carry current more efficiently than aluminum, allowing for less material to perform the same function. While aluminum is still a good conductor, wires made of aluminum must be 50-60% larger than corresponding copper wires to reach the same level of current-carrying capacity. Therefore, aluminum branch circuit wires are typically one size larger than copper wires of the same amperage rating, while service entrance conductors are two sizes larger than corresponding copper wires.
Thermal expansion is another factor that must be considered. Because copper has a lower coefficient of thermal expansion than aluminum, it will expand and contract less with the temperature changes that can occur with the flow of electricity. Aluminum’s greater coefficient of thermal expansion results in more movement, often loosening connections in the wiring system. These loose connections can lead to dangerous arcing situations, resulting in high levels of heat and the increased possibility of fire.
Copper also boasts greater ductility and malleability compared to aluminum. These mechanical properties make copper easier to work with during manufacturing processes, such as drawing into wires or shaping into intricate components. This feature of copper also makes it much easier to work with during the installation process as well. The fact that it’s malleable allows for it to be pulled and bent without increased risk of damage to the wires.
Joints and termination points are another area where the more malleable copper is superior to aluminum. While copper wires are compatible with almost all types of terminations and connections, aluminum wires can cause problems in some types of installations. Older aluminum wires were not compatible with the steel connectors used in switches, outlets, and breakers at the time, resulting in loose connections and arcing situations. Joining copper and aluminum wires also presents problems, as the connection of dissimilar metals can result in galvanic corrosion, which degrades the materials over time, resulting in dangerously poor connections.
Oxidation, commonly referred to as corrosion, is another issue with aluminum wiring. Most metals react with oxygen in the air to oxidize, resulting in a layer of corrosion that covers the surface of the metal. In our home’s wiring, oxidation on the surface of wires can inhibit the flow of electrons between connections, resulting in problems. While copper oxide can slow down the flow of electricity (it’s considered a semi-conductor), aluminum oxide is a fairly effective electrical insulator and essentially restricts the flow of electricity. Limiting the aluminum wire’s exposure to ambient oxygen, through the use of anti-oxidant paste (which coats the aluminum) or tightly made connections (which mechanically presses the aluminum against the other metallic materials, limiting the exposed surface area available for oxidation) is an effective strategy for preventing oxidation. Incidentally, many manufacturers recommend periodically inspecting aluminum connections and re-torquing them to spec as needed.
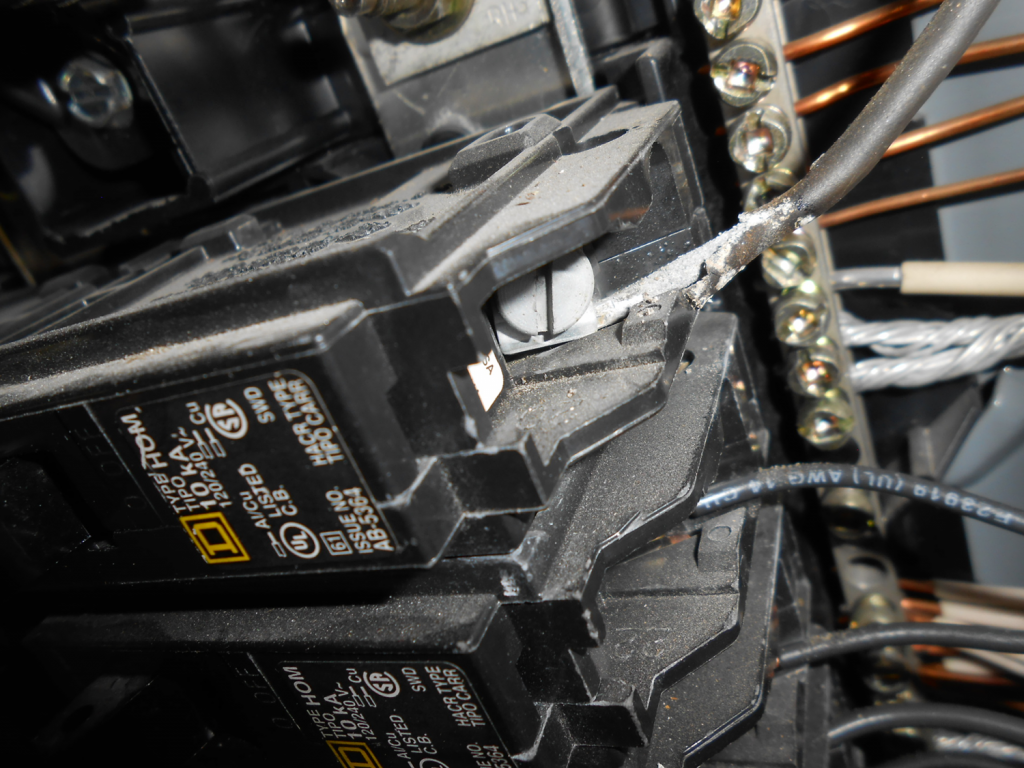
Not every aspect of aluminum wiring is negative, however. Aluminum is both cheaper and lighter than copper, making it the preferred choice of power companies for long-distance electrical transmission lines. The fact that the aluminum wire is lighter allows for smaller transmission towers as well, thereby lowering the upfront investment required to deliver power to utility customers.
While all these things are important considerations, the fact remains that most decisions regarding the type of materials that go into a home are based on price. Depending on the size of the home, using aluminum wiring instead of copper can save hundreds to thousands of dollars during construction. This non-trivial amount of money motivated most builders to choose aluminum wiring over copper, leading to eventual electrical issues and causing untold grief for home owners (and the home inspectors responsible for reporting on them.)
Inspectors are generally required to provide their clients with a minimal amount of information regarding their home’s electrical wiring, typically identifying the type of wiring system installed (e.g., non-metallic sheathed cable, knob and tube, cloth-covered wire, etc.) and whether solid aluminum wiring is present. It may be a better policy, however, to provide our clients with additional information regarding best practices for installing, maintaining, and repairing aluminum wiring and (as always) recommend evaluation by a qualified professional prior to the end of their inspection period.
Would you like to get an email every Friday where we share the newest things we’ve discovered about home inspections? CLICK HERE to sign up.
Want to be an Influencer in Your Field? Share This Post!
Thanks, Joe
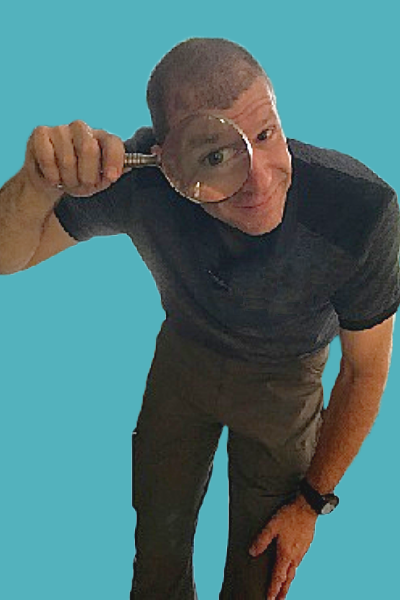